
THE BEGINNINGS
- Of Bavarian Brewery
THE BEGINNINGS
- Of Bavarian Brewery
ADS - From Newspapers
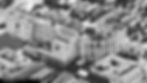
8A1 BAVARIAN BREWING CO. PLANT No. 1 (1949)
PLOT PLAN & LAYOUT
Please know that the plans shown below are best viewed on a large monitor or, at a minimum, a laptop or iPad; not a smart phone.
PLANT NO. 1: THE BLUEPRINTS
Shortly after Bavarian acquired Heidelberg Brewery in 1949, they had blueprints created of all of their structures that comprised their original and main plant, which was referred to as Plant No. 1. They were created by a draftsman, Frank C. Hall, who worked for Harold H. Hermann & Associates, Consulting Engineers, located in the Enquirer Building in Cincinnati, OH. Hall also created the blueprints for the Bavarian Plant No. 2, which was the former Heidelberg Brewery. These plans were acquired and provided courtesy of Timothy Holian, author of the "Over the Barrel" series about the brewing history in the Cincinnati area. The blueprint for the Plot Plan is shown below. Specific blueprints, photos and discussion of the Brew House for Plant 1 are in Section 8A2. The blueprints for all the other buildings - including the Stock Houses, Rack House, Wash House, Bottling Department, Boiler House, Large Stack, etc., are in Section 8A3. The blueprints were in relatively good condition for the last section noted and in Plant No. 2 but those for the Plot Plan and the Brew House showed greater deterioration requiring more restoration.
Plot Plan of Plant No. 1
The structures identified on the Plot Plan below (for Plant No. 1) are numbered in chronological order by the date they were built, as discussed previously in time periods 4. The Later Riedlin Years and 7. The Schott Brothers & WWII. They were constructed between 1903 and 1913. Buildings 1 and 2 are not shown because they were razed before Prohibition, and Buildings 7 - 9 are not indicated since they were located south of Lehmer Street and sold during Prohibition. Of those structures on the Plot Plan, only the Brew-Mill House (10) remains, which is why it is shaded amber below. As noted herein, it has been repurposed as part of the Kenton County Government Center (KCGC). The plot plan and aerial photo below were prepared for an exhibit near the main entrance of the KCGC.

Aerial Photo of Plant No. 1
The picture below corresponds to the Plot Plan above and provides another perspective of the brewery. Each structure was involved in different processes in the production and distribution of the beer, as described below.

BREWERY LAYOUT
In 1949, there were two groups of buildings that comprised the brewery complex, all lying south of Lehmer Street, as shown in the photo and diagram above. They are referred to as the lager east group (on the left) and the west group (on the right). These groups included the following buildings:
EAST GROUP
i) Brew & Mill House (10A & 10B),
ii) Maintenance & Storage Room, formerly the ice house (I) with lager cellar/tunnel
iii) Stock House (3A)
iv) Racking House, aka Stock House with Racking Room (3B)
vi) Wash House (3C)
v) Fermenting House, aka Stock House Addition (11)
plus a couple ancillary structures including a Retail Office and a Pitch Shed.
WEST GROUP
i) Bottling Department along with the Government Cellar (6),
ii) Boiler House (5)
iii) Tall Stack
plus a couple minor buildings including refrigeration and storage rooms.
Besides the 9 or 10 main buildings, there were a few ancillary structures, or a total of about 14 different building names. In addition, most of the building floors had different names, e.g. Fermentation Cellars A - C and Storage Cellars A - D and there were some different rooms on the floors, such the Tap Room, Main Offices, Filter Room, etc. There was also a parking lot on the northwest corner of Lehmer and (short) Main Street - not shown on the Plot Plan.
An explanation for having two separated groups for buildings is that the brewing of beer was required to be separate from the bottling of beer, according to federal regulations. However, these two building groups were connected underground by tunnels. One tunnel extending from the Stock/Rack House to the Bottling Department transferred beer ready to be consumed through underground tubes in the tunnel to the Government Cellar for calculating state and federal tax before the beer was then bottled and canned in the Bottling Department and transported. Under the Maintenance building, which was formerly an Ice House, was an old lager cellar that became another tunnel that also connected to the Bottling Department. Before prohibition, there was a third tunnel that extended north to a building on W. Pike Street that was the former Bottling Department. This tunnel was apparently abandoned after Prohibition. (See section 4A. Brewery Tunnels.)
Essentially, the brewery access to Plant No. 1 was divided into two parts:
1) The grain delivery and an office access were from W. 12th Street. Management was primarily located in offices on the second and third floors of the Brew - Mill House and used this access, as did most customers and guests.
2) The shipping of beer and return of bottles/kegs and the shipping of beer and the entrances for most brewer workers (non-office personnel) were from Lehmer Street.
The aforesaid operations were supported via the Engine Room on the bottom of the Mill House and the Boiler Room (5) next to the Bottling Department. In addition, refrigeration was supplied by condensers on top of the Bottling Department with cooling also supplied by the Brine Room, on the top floor of the Fermenting House, aka Stock House Addition.
HOW THE STRUCTURES OPERATED AS A BREWERY
Even though the buildings are labeled chronologically, the brewing process began with the Brew & Mill House (10A & 10B) in the largest East Group of buildings, and then proceed to the east, or from right to left, and then from left to right to the West Group of buildings, and back to a couple buildings in the East Group, as summarized below.
MAIN EAST BUILDING GROUP
1st: Mill House (10B) & Brew House (10A) - producing a Liquid Wort
2nd: Stock Houses - Fermentation Cellars & Yeast Tubs on Top Floors (3A & 3B)
3rd: Stock Houses - Storage Cellars on Lower Floors (3A & 3B)
WEST BUILDING GROUP
4th: Bottling Department (5) - to the Government Cellar for Taxes Connected to Tunnel
Filling Bottles and Cans & the Distribution via trucks
5th: Bottling Department (5) -Cleaning bottles
EAST BUILDING GROUP
4th: Racking Room - Filling Barrels on Ground Floor (3B) & Distribution via trucks
5th: Wash House and Pitch Shed (3C) - Cleaning & Repairing Barrels
6th: Retail Office (next to 3C) - controlling trucks delivering & picking up barrels, bottles and cans.
SUPPORT
EAST BUILDINGS - Maintenance Building (I) & Mechanical Room in Mill House (10B)
WEST BUILDINGS - Boiler Room (6), Tall Stack (4) and Refrigeration & Storage Rooms
The grains used for brewing were stored and milled in the Mill House, and then transferred to the Brew House. A liquid wort was then created in the Brew House. (Please see information and blueprints for 8A2. Brew & Mill House.) It was then transferred to the Fermenting Cellars on the top floors of the Stock Houses.Once the fermentation process was over, the beer was stored in the Stock Cellars of the Stock Houses before it was bottled, canned or filled into barrels. (Please see information and blueprints for the 8A3. Other Buildings.) The brewery complex was supported by an Mechanical Room on the bottom floor of the Mill House and a Boiler Room on the far west side of the site.
THE PHYSICAL CAPACITY OF PLANT NO. 1
A few years after the above blueprints were created, a local resident, C.B. Truesdell, prepared a detailed history of the Bavarian Brewing Co., including a summary of the capacity of each of the Bavarian's two plants. Below is the capacity of Plant No. 1 as of 1954. The capacities of the Fermenting and Stock Cellars appear to be corroborated by the blueprints, and did not appear to have any material changes between 1950 and when the brewery closed in 1966. However, there were improvements to the brewery as previously noted herein in the mid 1950s up until around 1960, which helped increase brewing production and improved the bottling and canning and operations. The equipment that was in used when the brewery closed in 1966 may be viewed in the auction catalog.
Brew House:
-
a Brew Kettle with a capacity of 350 barrels, and a lauter tun and pump
-
a Cereal Cooker with 2,325 gallons capacity
-
a Mash Tun with a capacity of 235 barrels (Replaced with a Lauter Tun)
-
two grinding Mill Scale Hoppers with capacities of 455 bushels and 235 bushels each
-
an American Peerless Malt Mill
-
three Hot Water Tanks, one with a capacity of 5,270 gallons; the others with capacities of 412 barrels each
Fermenting Rooms/ Cellars: (39 fermentation tanks with a total of 10,160 barrels)
-
A) 14 wood tanks with capacities of 220 barrels each, and four with 125 barrels each (2,450 barrels)
-
B) 10 steel tanks with capacities of 200 barrels each (2,000 barrels)
-
C) 11 steel tanks with capacities of 310 barrels each and three with 390 barrels each (4,580 barrels)
Stock Cellars: (83 beer storage tanks with a total of 28,170 barrels)
-
A) 32 tanks with 208 barrels each (6,656 barrels)
-
B) 13 tanks with 535 barrels each and one with 375 barrels (7,330 barrels)
-
C) Seven tanks with 222 barrels each and five tanks with 200 barrels (2,554 barrels)
-
D) 13 tank with 470 barrels each (6,110 barrels)
-
E) 12 tanks with 460 barrels each (5,520 barrels)
All the storage tanks were made of steel and glass lined.
Storage Bins for Malt:
-
Three with capacities of 95,000 pounds, 85,000 ponds and 55,000 pounds. (235,000 pounds total.)
Other Machinery:
-
Six beer filters
-
a Wash House with a filtered washing machine and a tank with a capacity of 150 barrels
-
a pitching barrel machine
-
a Racking (filling) Room capable of filling 70 barrels an hour
-
18 gas storage tanks with 250 pounds of pressure each
-
a beer cooler capable of cooling 160 barrels per hour
-
a wood tank and hops strainer holding 400 barrels
Government Cellar:
-
Five tanks with a capacity of 240 barrels each (1,200 barrel total)
John Collins was the agent in charge and federal taxes were assessed at $9 per barrel.
Please see Section 8A2 for blueprints, photos and discussion of the Brew House for Plant No. 1.
PLANT NO. 2 (Former Heidelberg Brewery)
For information about the second Bavarian plant, please see 8B. Plant No. 2 Floor Plans & Equipment.
In comparison to Plant No. 1, which could produce about 225,000 barrels annually in 1949, Plant No. 2 could produce a little more than one-half this production, or about 120,000 barrels annually. However, the Bavarian Plant site, building size and stock storage was slightly more than twice that of Plant No. 2.
SOURCES:
Timothy Holian, for a copy of the original Plot Plan.
Behringer-Crawford Museum, for the Aerial Photo.
C.B. Truesdell, (The History of) The Bavarian Brewery, 1954. (Unpublished manuscript.)
The Riedlin and Schott families, for information.
Dave Gausepohl, who provided information on the gravity system used by the brewery.
Newspapers.com and Cincinnati Enquirer.
Newsbank, Inc. and the Kentucky Post.
The background is an aerial photo of th Bavarian Brewing Co. Plant No. 1 around 1950.
